NEWS
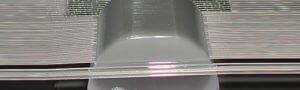
Wire sawing, whether using abrasive slurry or diamond wire, offers distinct advantages over other cutting methods in many applications. The high precision, reduced kerf loss, and reduced damage of wire sawing can have a substantial effect not only on the cutting process, but also on downstream operations. REDUCED KERF LOSS: The first advantage of wire sawing is reduced kerf loss (the material lost during cutting). Compared with ID saws (0.300 to 0.500mm kerf) and diamond blade saws (0.200 to 3.00mm), a multi wire saw can produce kerfs of less than 0.200mm with slurry, and 0.15 to 0.26mm with diamond wire. This material savings add up; after spending substantial time and money growing a perfect crystal or other material, reducing kerf loss helps save precious material and increase yields. REDUCED DAMAGE: Wire sawing is a relatively gentle process, particularly when cutting with slurry. The gentle, low-force cutting action and fine abrasive leads to reduced depth of damage on the cut surface. This reduction in sub-surface damage means less stress in the material and less material that needs to be ground, lapped, or polished after slicing. Once again this saves material, and reducing the amount of removal necessary after slicing means a customer can cut thinner pieces, further improving yields and lowering cost. The reduced damage also extends to the entry and exit points of the cut – the gentle cutting action means less chipping or other physical damage, leaving clean corners and improving quality. Even cutting with diamond wire, a more aggressive process than slurry, is quite gentle relative to other cutting methods, so many of the same benefits apply. BETTER GEOMETRY : A goal of any cutting method is to create flat, consistent pieces, and here a wire saw excels. TTV, bow, and warp are all minimized. This again reduces the need for post-processing, improving yields. HIGHER THROUGHPUT: On the surface, wire sawing is slow. The trade off of such a gentle cutting method is that the machine moves through the workpiece slowly, so cycle times are long. Despite this, wire sawing is actually very efficient due to the use of multiple wires. A production machine can have hundreds of wires contacting the workpiece simultaneously. As a result, at the end of a single cutting cycle the entire length of material will be completed. On particularly hard materials, using diamond wire can significantly improve throughput, though it can also raise the cost per slice. We examine each application to find the most efficient process. Wire sawing is an excellent solution to many of the challenges facing companies looking to produce wafers and other thin pieces from delicate, valuable, and very hard materials. It is the best solution for slicing silicon carbide, sapphire, GaN, glass, ceramics, and more. Contact GTI today to learn how wire sawing can work for your application.
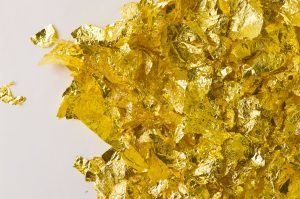
Many semiconductor devices particularly those made with gallium arsenide (GaAs) or indium phosphide (InP), require the removal of metal layers by etching. Gold, for example, difficult and expensive to remove by etching due to its inertness. Lift off provides an alternative to etching. A pattern is first created in a sacrificial layer of photoresist before the gold is the deposited. The gold adheres strongly to the underlying device layers of GaAs (or deposited insulating layers,) and also to the photoresist which does not adhere as strongly to the device layers. Standard lift-off processes use solvents to remove the resist, and often take the gold with it. The main problems with this process are: redeposition of the gold from the solution onto the wafer, disposal of the solvent is expensive, and reclaiming the gold from the solvent is not easy and it is too costly to throw away. Takatori’s AMR-2200G system provides an effective alternative that does not use solvents! The system applies an adhesive tape to the wafer surface and then lifts it off in a controlled manner designed to match the specific device requirements. The gold on the photoresist is removed with the resist, while the gold adhered to the underlying device layers remains on the wafer surface undisturbed. Benefits of this lift off with tape are: eliminates potential for gold being redeposited on the wafer surface, lowers overall cost since no solvent disposal is need, and makes it easy to reclaim the gold from the roll of tape. This process is used successfully by many GaAs device fabricators. It can be used with many different metals; including gold, indium, and aluminum. Contact GTI today to learn more about Takatori’s tape-based liftoff solution and how it can improve your bottom line.
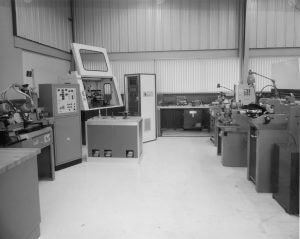
For 40 years, GTI has been evolving to provide advanced manufacturing solutions to its customers. When the company opened its doors on Oct. 1, 1978, Grinding Technology Inc. focused not only on importing leading-edge metalworking equipment from Europe to the United States; but also on supporting customers once their machines were up and running. About 10 years later, the company began to branch out into the semiconductor industry, working with GMN to sell wafer grinders. This included the MPS-T500, the first fully automatic, cassette to cassette wafer backgrinder brought to market. In order to provide a complete solution to semiconductor companies, GTI entered a partnership with Takatori to provide tape, detape, and mounting equipment in 1989. As the business evolved and the semiconductor industry continued to grow, Grinding Technology Inc. re-branded itself as GTI Technologies, Inc., in 1997 reflecting its diversification. The partnership with Takatori also grew deeper as GTI began to offer their new multi wire saws. By 2000 GTI’s business was almost solely focused on the semiconductor and advanced materials businesses, and this remains our focus today. GTI led the way to develop wire slicing of mono-crystalline sapphire and silicon carbide. Working together with customers, GTI helped to pave the way for the blue and white LED revolution, and played a key role in the rapid growth of today’s advanced power devices. The company continues to provide advanced solutions for leading semiconductor companies in North America and Europe. We thank our customers and our suppliers for their support over the last 40 years, and we look forward to working together to make a better future.
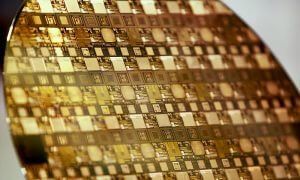
Developments in advanced packaging and 3D integration have driven the demand for better ways to work with ultra-thin wafers safely. The need to run thin wafers through processes beyond the standard post-grinding steps (like polishing, detaping and dicing) has driven demand for cost-effective ways to bond ultra-thin wafers to a carrier made of sapphire, glass, silicon, or other materials. Many temporary bonding methods have featured spin-on adhesive, which requires complex, expensive machines. In 2003, Takatori began offering its WSM-series machines, providing a unique temporary bonding solution featuring double-sided tape. Unfortunately, the double-sided tapes available at that time were not capable of surviving high-temperature processes, and this limited the appeal of Takatori’s new machine. Fortunately double-sided tapes have continued to evolve, and today both Nitto’s Revalpha and Sekisui’s Selfa tapes can survive higher temperatures while maintaining good adhesion and allowing for easy debonding. Today, Takatori’s WSM-100 offers a cost-effective solution for temporary bonding. The machine uses a combination of atmospheric lamination and vacuum bonding, and works with many types of carrier wafers and different tapes. Today’s tapes are either heat-release or UV-release, and both types are supported by Takatori’s debonding/mounting tool, the WSM-200. Call GTI Technologies today at +1 (203) 929-2200 or contact us via the web at gti-usa.com to find out how the WSM-series of machines can address your temporary bonding needs.