METAL LIFTOFF
Metal liftoff is a critical component in the semiconductor manufacturing process, allowing for the precise removal of excess metal from substrates. At GTI Technologies, we are ready to provide you with qualified experts to help you through the whole process. Remember, this technique is essential for creating intricate circuit patterns on semiconductor wafers, ensuring clean lines and reliable electrical connections. By adopting advanced metal liftoff methods, manufacturers can significantly improve the accuracy and efficiency of their production lines, resulting in high-quality electronic devices. The process of metal liftoff not only enhances the functionality of the components but also increases yield by minimizing material wastage.
Industries Benefiting from Precision Metal Liftoff
Numerous industries can reap the advantages of precision metal liftoff, particularly those producing sophisticated electronics where detail and accuracy are paramount. Businesses can ensure the integrity of their circuits and connections by working with our supplier of manufacturing equipment capable of handling the intricacies of metal liftoff. This advanced technique is a staple in semiconductor equipment, where unwanted metal is removed with precision to avoid damaging delicate components.
Machine | Wafer Size | Throughput | Machine Size (WxDxH) |
---|---|---|---|
AMR-2200G | Up to 200mm, 300mm can be discussed | Up to 40wph, application dependent | 1100mmx1025mmx1650mm |
AMR-2200G:
Remove excess gold or other metals from a wafer’s surface using a simple, effective, tape-based process. No solvents or other chemistry required, and the often valuable metals can be more easily reclaimed from the waste tape. Save money and time by maximizing reclaim and reducing costs by eliminating chemical handling and disposal.
The Metal Liftoff Process
Here is a quick overview of how our sophisticated metal liftoff process works:
An Effective Alternative to Chemical Etching
Many semiconductor devices, particularly those made with gallium arsenide (GaAs) or indium phosphide (InP), require the removal of metal layers by etching. Gold, for example, is difficult and expensive to remove by etching due to its inertness. Lift-off provides an alternative to etching. A pattern is first created in a sacrificial photoresist layer before the gold is deposited. The gold adheres strongly to the underlying device layers of GaAs (or deposited insulating layers) and the photoresist, which does not adhere as strongly to the device layers.
Standard lift-off processes use solvents to remove the resist and often take the gold with it. The main problems with this process are:
- re-deposition of the gold from the solution onto the wafer,
- disposal of the solvent is expensive, and
- reclaiming the gold from the solvent is not easy, and it is too costly to throw away.
Takatori’s AMR-2200G system provides an effective alternative that does not use solvents! The system applies adhesive tape to the wafer surface and then lifts it off in a controlled manner designed to match the specified device requirements. The gold on the photoresist is removed with the resist, while the gold adheres to the underlying device layers and remains undisturbed on the wafer surface. The benefits of this lift-off with tape are:
- eliminates the potential for gold being redeposited on the wafer surface,
- lowers overall cost since no solvent disposal is needed, and
- makes it easy to reclaim the gold from the roll of tape.
Many GaAs device fabricators use this process successfully. It can be used with many metals, including gold, indium, and aluminum. In addition, our
metal-cutting wire tools are utilized to execute fine cuts that traditional methods cannot achieve, further highlighting the precision capabilities of metal liftoff in cutting-edge manufacturing processes.
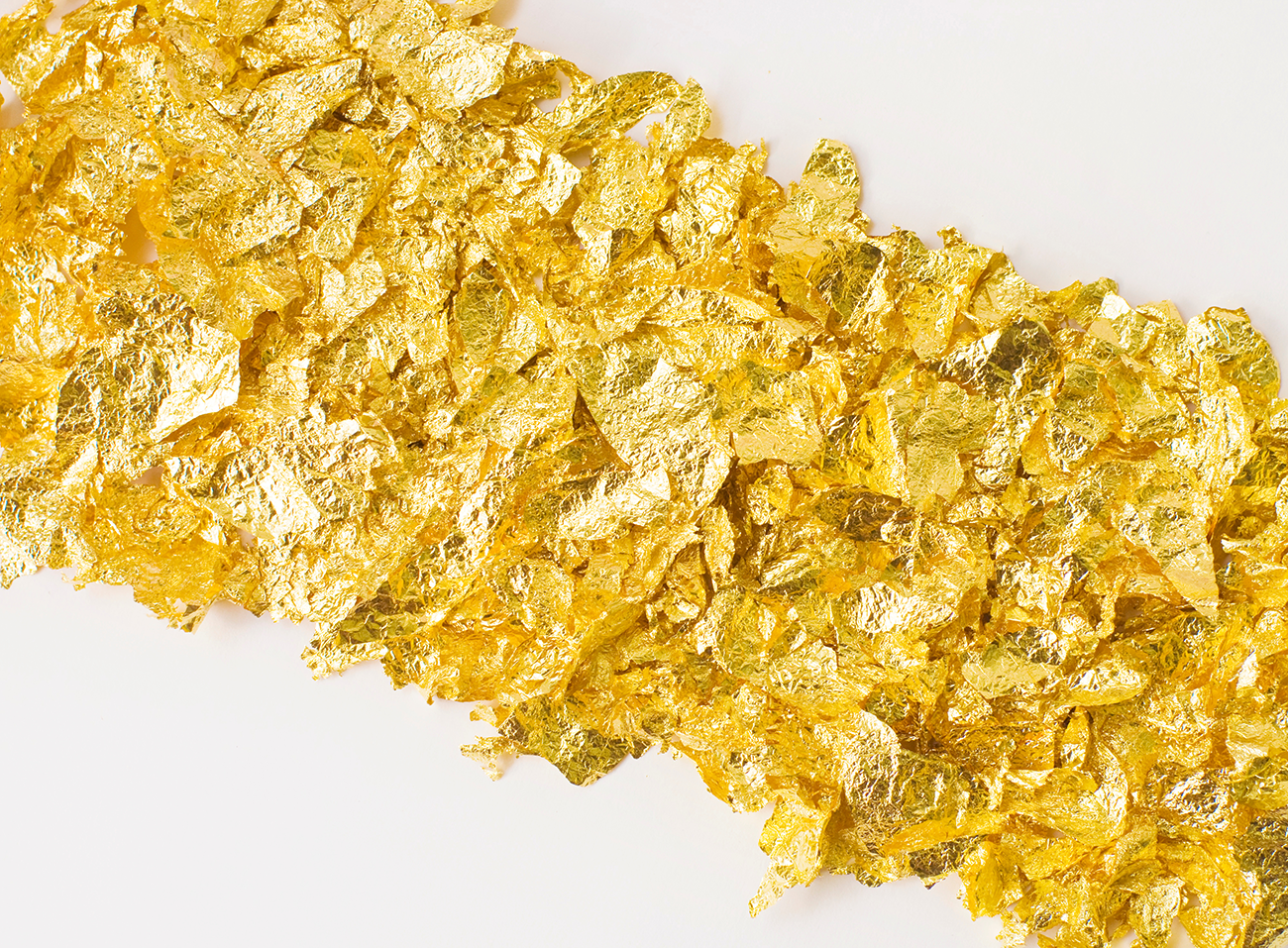
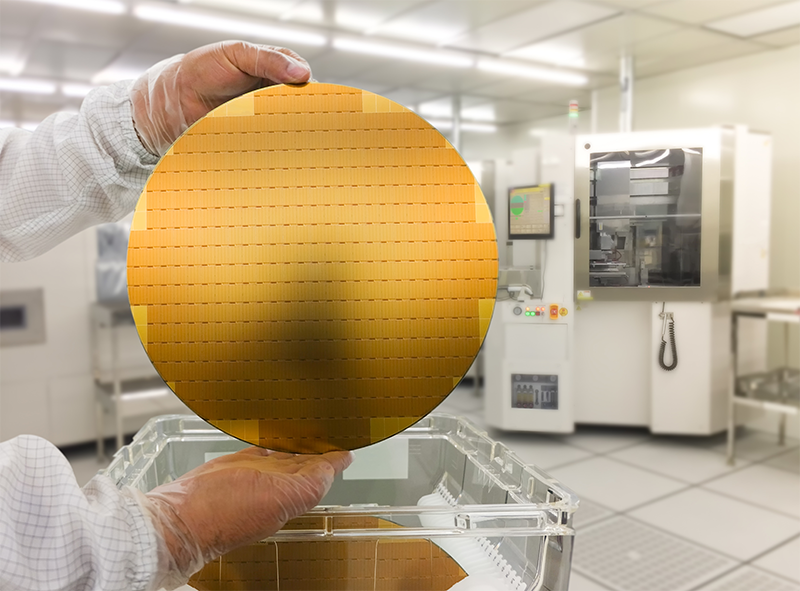
Get a Quote for Metal Liftoff
If your enterprise wants to enhance its manufacturing process with precise and reliable metal liftoff capabilities, we are here to help. Our state-of-the-art services are designed to meet the demanding standards of semiconductor production and beyond. Ready to get started and transform your production line? Learn more about us, and reach out to our expert team today and get a quote for metal liftoff. Our team is committed to providing tailored assistance and delivering exceptional results that align with your precise manufacturing needs. Contact us today!