Wire sawing, whether using abrasive slurry or diamond wire, offers distinct advantages over other cutting methods in many applications. The high precision, reduced kerf loss, and reduced damage of wire sawing can have a substantial effect not only on the cutting process, but also on downstream operations.
REDUCED KERF LOSS:
The first advantage of wire sawing is reduced kerf loss (the material lost during cutting). Compared with ID saws (0.300 to 0.500mm kerf) and diamond blade saws (0.200 to 3.00mm), a multi wire saw can produce kerfs of less than 0.200mm with slurry, and 0.15 to 0.26mm with diamond wire. This material savings add up; after spending substantial time and money growing a perfect crystal or other material, reducing kerf loss helps save precious material and increase yields.
REDUCED DAMAGE:
Wire sawing is a relatively gentle process, particularly when cutting with slurry. The gentle, low-force cutting action and fine abrasive leads to reduced depth of damage on the cut surface. This reduction in sub-surface damage means less stress in the material and less material that needs to be ground, lapped, or polished after slicing. Once again this saves material, and reducing the amount of removal necessary after slicing means a customer can cut thinner pieces, further improving yields and lowering cost.
The reduced damage also extends to the entry and exit points of the cut – the gentle cutting action means less chipping or other physical damage, leaving clean corners and improving quality.
Even cutting with diamond wire, a more aggressive process than slurry, is quite gentle relative to other cutting methods, so many of the same benefits apply.
BETTER GEOMETRY :
A goal of any cutting method is to create flat, consistent pieces, and here a wire saw excels. TTV, bow, and warp are all minimized. This again reduces the need for post-processing, improving yields.
HIGHER THROUGHPUT:
On the surface, wire sawing is slow. The trade off of such a gentle cutting method is that the machine moves through the workpiece slowly, so cycle times are long. Despite this, wire sawing is actually very efficient due to the use of multiple wires. A production machine can have hundreds of wires contacting the workpiece simultaneously. As a result, at the end of a single cutting cycle the entire length of material will be completed.
On particularly hard materials, using diamond wire can significantly improve throughput, though it can also raise the cost per slice. We examine each application to find the most efficient process.
Wire sawing is an excellent solution to many of the challenges facing companies looking to produce wafers and other thin pieces from delicate, valuable, and very hard materials. It is the best solution for slicing silicon carbide, sapphire, GaN, glass, ceramics, and more. Contact GTI today to learn how wire sawing can work for your application.
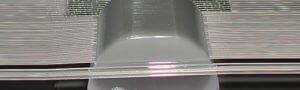