Diamond wire, originally adopted for mass production by the sapphire industry and then by the silicon industry, significantly increases the productivity of wire sawing and provides downstream benefits as well. It also offers an interesting option for cutting composite materials: demonstrating advantages when cutting both core materials and carbon fiber.
Diamond wire is made in a number of ways, but the most common way is by attaching fine diamond particles to steel wire through an electroplating process. Wire manufacturers provide the nominal diameter of the wire and the diamond abrasive, as well as the core diameter (the diameter of the wire itself) and the size of the abrasive particles. While the most commonly used wires don’t offer high diamond density, wire makers can fine tune the abrasive density and some offer particularly high-density diamond wire for special applications. Resin-bonded diamond wire is also available, though it is less common.
Advantages of Diamond Wire: Fast, Clean, Gentle
The first advantage of diamond wire is speed. Conventional slurry-based wire sawing can be slow when cutting very hard materials. Diamond wire offers substantial improvements in speed, increasing the productivity of each machine.
Next, diamond wire is clean. The coolant required for cutting is primarily water, with a small amount of surfactant added. This makes for easy set up, and also makes it easy to reclaim material lost during the cutting process.
Finally, while diamond wire is more aggressive than slurry for cutting crystalline materials, it is a relatively gentle process for cutting composites. It allows for very fine edges on core materials, less deformation of metallic core, and when cutting carbon fiber it offers lower damage, less delamination, and higher surface quality.
Contact GTI today to learn more about how diamond wire may help you with your applications.
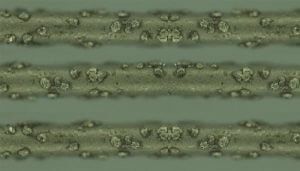