Wafer Lamination
Wafer lamination is a critical process in semiconductor manufacturing that ensures the protection and integrity of wafers as they undergo various stages of production. At GTI Technologies, we understand that wafer lamination entails the application of a laminating film over the wafer's surface to create a barrier that guards against contaminants, mechanical stress, and other environmental factors that could compromise the wafer's quality. Proper wafer lamination is essential for maintaining the uniformity of the wafer throughout the manufacturing process, which in turn is crucial for the functionality and reliability of the semiconductor devices.
How to Achieve Precision and Uniformity with Wafer Lamination
Achieving precision and uniformity with wafer lamination requires working with our state-of-the-art supplier of manufacturing equipment. Our film laminator is designed for delicate handling and application. Such equipment ensures that the semiconductor equipment used in the lamination process adheres to strict industry standards. On the other hand, vacuum lamination is particularly effective in creating a bubble-free and uniform layer, which is vital for the success of further processing steps such as photolithography and etching. Advanced film laminator systems are utilized for precision control, allowing for exact film tension and placement. Additionally, using high-quality backgrind and tape lamination materials further enhances the wafer's stability and readiness for subsequent fabrication phases.
Our Process
01.
Work together with our customers and suppliers to clearly understand the application and our customer’s needs and potential solutions.
02.
Test our preferred solution, evaluate with the customer.
03.
Present and then deliver solutions on-time.
04.
Support our customers with training, spare parts, and ongoing engineering resources.
Discover Our Advanced Wafer Lamination
Explore our comprehensive wafer lamination solutions and discover how our advanced techniques can benefit your semiconductor equipment manufacturing process. Our expertise in wafer lamination ensures that your wafers are laminated with the utmost precision, providing a consistent and protective layer necessary for high-quality device production. For more information about our wafer lamination techniques and services, navigate our about us page. If you want to use our sophisticated wafer lamination services or have any questions, contact us today. Our team is dedicated to supporting your operations with superior wafer lamination solutions that drive productivity, enhance quality, and meet the needs of even the most stringent semiconductor applications.
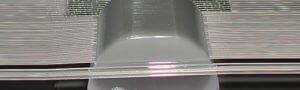
Contact us
Hours
Monday - Friday: 8AM-5PM
Service Area
6 Armstrong Road,
Shelton, CT 06484, USA