Metal Cutting Wire
Metal cutting wire is an essential tool in precision manufacturing, offering high accuracy and efficiency in cutting various metal materials. At GTI Technology, our metal cutting wire is renowned for its versatility and strength. This makes it the ideal choice for industries that require clean and precise cuts, such as electronics, automotive, and aerospace engineering. With the right metal cutting wire, manufacturers can ensure smooth edges and exact dimensions, enhancing the quality of the final product. The application of metal cutting wire in complex and delicate operations has become increasingly important as industries push for higher precision and reduced waste in their manufacturing processes.
Why Choose Metal Cutting Wire?
Choosing the right metal cutting wire is vital for achieving the best results in your cutting tasks. High-quality metal cutting wire from our renowned supplier of manufacturing equipment can substantially increase the efficiency and precision of your production line. Whether using multi-wire saws for slicing semiconductor wafers or intricate metal components, the right wire will provide a consistent cut and long service life. With our exceptional wire sawing techniques, metal cutting wire also enables the production of complex shapes and narrow kerfs that would be challenging to accomplish with other cutting methods. Its ability to withstand high tension and resist wear translates into reliable operation and reduced downtime. If you need a dependable and precise cutting solution, place your order for our high-quality metal cutting wire today. We are committed to supplying only the best metal-cutting wire solutions tailored to meet the specific demands of your industry.
Our Process
01.
Work together with our customers and suppliers to clearly understand the application and our customer’s needs and potential solutions.
02.
Test our preferred solution, evaluate with the customer.
03.
Present and then deliver solutions on-time.
04.
Support our customers with training, spare parts, and ongoing engineering resources.
Place Your Order for a Metal Cutting Wire
Each wire is designed to deliver exceptional performance and longevity, ensuring that your cutting operations run smoothly and efficiently. Please contact us for more information on our metal-cutting wire options or to discuss how they can enhance your production capabilities. Our team is ready to provide expert advice and support, helping you select the perfect metal cutting wire for your precision manufacturing needs. With our superior metal cutting wire, you can expect outstanding results in all your cutting endeavors.
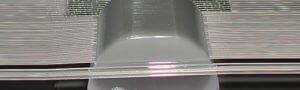
Contact us
Hours
Monday - Friday: 8AM-5PM
Service Area
6 Armstrong Road,
Shelton, CT 06484, USA